Linear Type Opp Labeling Machine
The hot melt glue labeling machine is designed for high-speed labeling of round containers. Applicable to the labeling for both empty bottle and filled bottles.
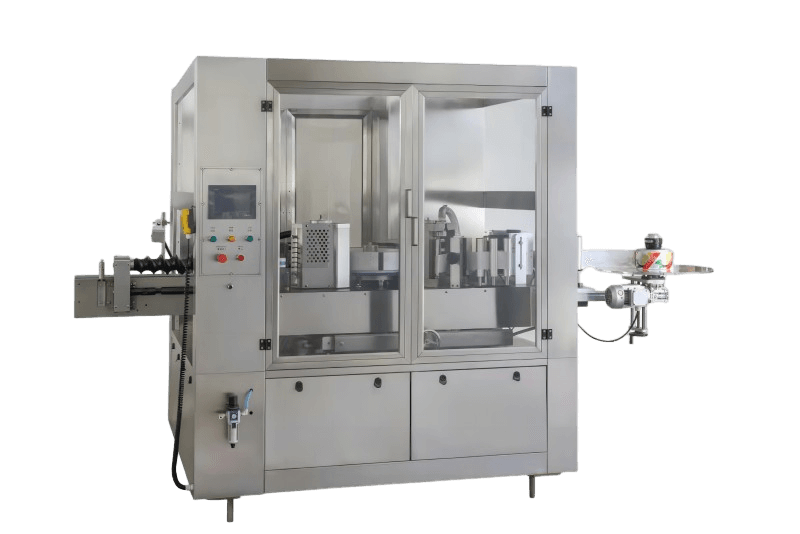
Technical Parameter
Model | OPP-8L |
Labeling speed | 6000-18000BPH |
Labeling material | OPP/BOPP |
Applicable diameter of bottle | Ø40- Ø105mm |
Applicable height of bottle | 80-350mm |
Applicable label length | 125-325mm |
Applicable label height | 20-190mm |
Air consumption | 0.2m3/min |
Air compression | 5-8Bar |
Glue Comsumption | 1KG glue for 100000pcs(label height at 50mm) |
Power supply | 8KW |
Voltage | 380V,50HZ |
Overall dimension | L3150mm×W1270mm×H1850mm |
Weight | 1500Kg |
Electric Configuration
PLC | Schneider/France |
Touch Screen | Schneider/France |
Sensor | SICK/Germany |
Servo system | Schneider/France |
Encoder | SICK/Germany |
Promixity switch | Schneider/France |
Contactor | Schneider/France |
Low voltage electrical appliances | Schneider/France |
Security Moule | Schneider/France |
Limit switch | Schneider/France |
Adapter | Schneider/France |
Relay | Schneider/France |
Machine Introduction&Features
Our In-Line Labelers are specifically designed for labeling round containers with the use of roll-fed OPP labels. With a capacity of up to 300 bpm, they are suitable for modest output requirements. Our Hot Melt Glue Labelers are versatile machines, designed and manufactured for various industries, including Food, Beverage, Craft Brewery, Coatings & Chemicals, Personal Care, Wine & Spirits, Converting, and Molded Fiber applications.
This machine is designed with a linear conveyor belt that moves products through the labeling process.
This machine uses a hot melt glue system to apply labels onto products. The hot melt glue is heated and then applied to the label, which is then attached to the product.
Can be used to label a variety of different products, including bottles, jars, cans, and other containers.
The machine is designed with a user-friendly interface that makes it easy to operate and adjust the labeling settings.
Servo driven output for fast and accurate delivery.
The linear type hot melt glue labeling machine is designed to apply labels with a high degree of accuracy and precision, ensuring that each label is applied in the correct position and orientation.
The machine is designed for easy maintenance and cleaning, with components that can be easily accessed and removed for cleaning or replacement.
Product Gallery
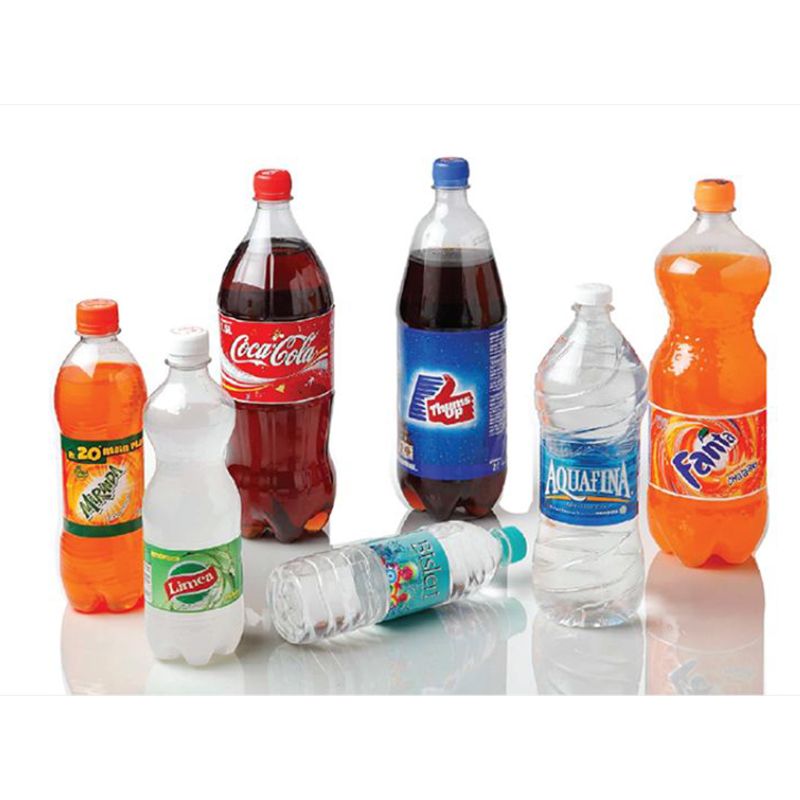
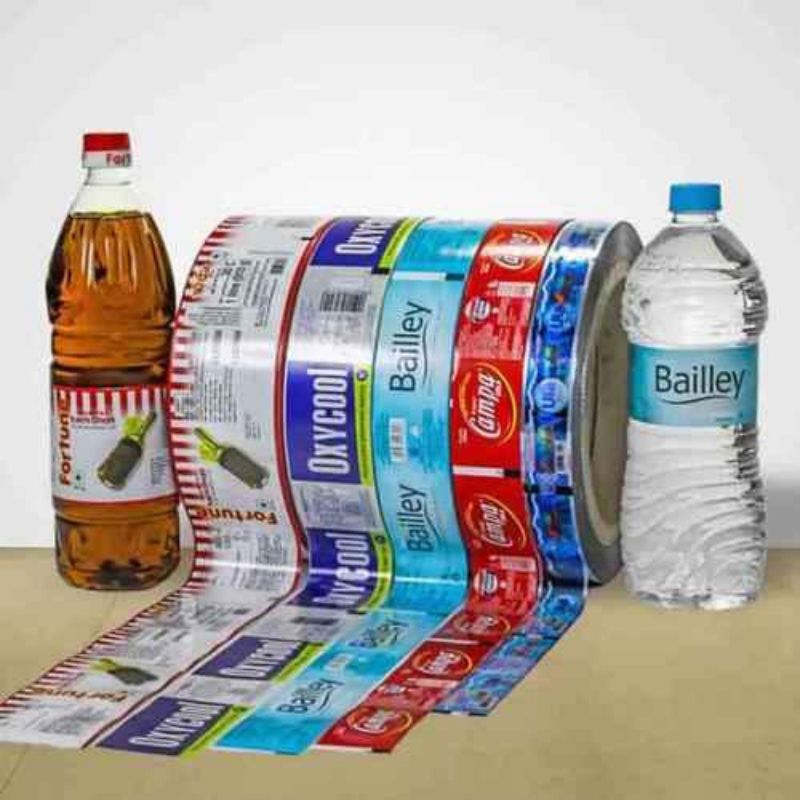
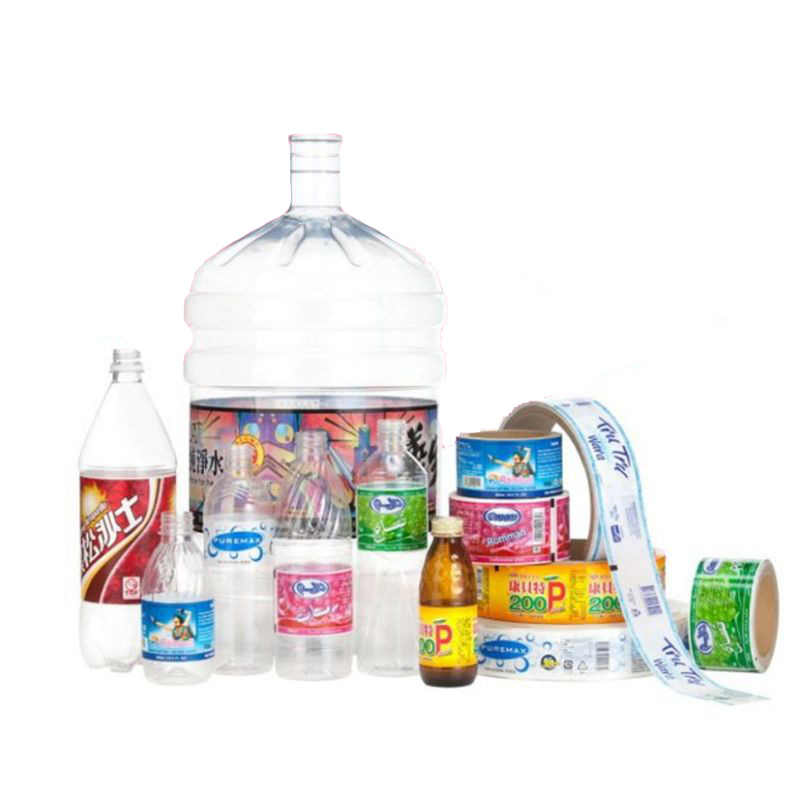
Product Details
Name | Description | |
---|---|---|
![]() |
Label Dispenser Tray | Holds the labels, typically located on the top or side of the machine. The main function of the supply label tray is to provide a place to contain labels and to feed them through the machine's feeding system to the labeling head for applying labels onto products or packaging. |
![]() |
Label Cutting Device | The cutting knife group performs the function of cutting off the label from the label material, after which the label is feeding to the suction roll for further processing. The label is securely clamped by the combination of a moving knife and a static knife, and then transported to the suction roll in a stable manner by utilizing a combination of suction and blowing forces. |
![]() |
Label Suction Device | It picks up the label from the feeding area and transfers it to the labeling position by rotating and suctioning. |
![]() |
Bottle Feeding Device | The bottle divider on the hot melt glue labeling machine transports bottles from the supply area to the star wheel and ensures even distribution. Protrusions on the star wheel clamp the bottles and carry them to the labeling position. |
![]() |
Automatic Label Correction | It involves a sensor or vision system that detects the position of the label on the labeled object. If the label is detected to be misaligned or skewed, the Automatic Label Correction system will automatically adjust the position of the label or the timing of the labeling cycle to ensure that the label is applied correctly on the next labeled object. |
![]() |
Bottle Rubbing Mechanism | The bottle rubbing mechanism causes the bottle to rotate as it passes through the cavity formed between the rubbing mechanism and the labeling drum surface, thereby allowing the label to wrap around the bottle. |
![]() |
Hot Melt Glue Coating Device | It generally consists of a coating roller, hot melt glue tank, hot melt glue supply system, and other parts. The coating roller applies hot melt glue evenly on the back of the label, the hot melt glue tank provides storage and heating of the hot melt glue, and the hot melt glue supply system controls the supply volume and speed of the hot melt glue to ensure quality and efficiency of coating. |
![]() |
Touch Screen | The touch screen also displays real-time information about the labeling process, such as the status of the labeling cycle and any errors or malfunctions that may occur. This information can help the operator quickly identify and resolve any issues that may arise during the labeling process. |
![]() |
Electronic Cabinet | The control cabinet receives signals from sensors, the touch screen interface, and other components of the machine, and then processes this information to control the labeling process. It controls the movements of the labeling head, the cutting knife, the conveyor belt, and other components of the machine to ensure accurate and consistent labeling. |
FAQs
Our labeling machines are versatile and can label a variety of products, including round objects,suqare objects and objects with flat surface etc.
There are sleeve labeling machine,hot melt glue labeling machine,self-adhesive labeling machine and cold glue labeling machine,can meet your different labeling request.
Yes, our labeling machines are compatible with various container materials, including plastic, glass, and metal.
Yes, it can handle various label sizes and shapes, including wrap-around, front and back, and top and bottom labels.
Our labeling machines use advanced sensors and precision mechanics to ensure accurate label position, even on irregularly shaped containers.
Yes,our engineer will provide free design for your checking before make the final quotation.
Lead time varies depending on the specific machine and production schedule, but typically takes 6-8 weeks.
We accept a variety of payment methods, including wire transfer, credit card, and PayPal.
We offer online technical support and troubleshooting services for the lifetime of our machines, as well as parts and service support.
Yes, we provide free online training for machine operation and maintenance to ensure our customers can use and maintain machines effectively.
We offer a 1-year warranty for all of our machines, with additional warranties available upon request.
Get Your Free Quote Now!