Big Bottle Blow Molding Machine
The large bottle blow molding machine is an efficient, speedy, and convenient solution for producing a wide variety of bottles under 20 liters. With its versatile capabilities, it can create bottles for various industries, including food packaging, edible oil, soda and mineral water, fruit juice, wine, cosmetics, and more. Whether you need a high volume of bottles or a customized design, this machine can meet your production needs with ease.
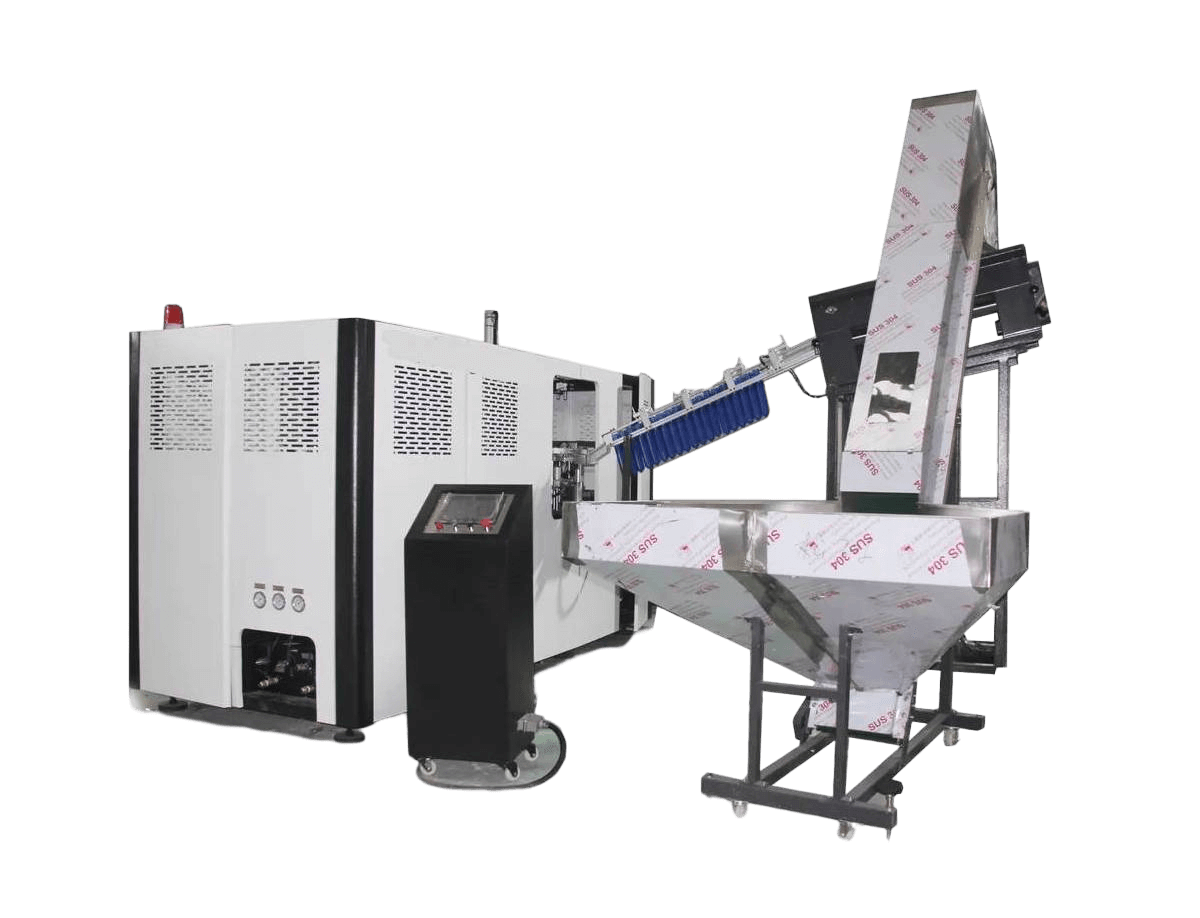
Technical Parameter
Model | BS5-2 | BS-10L-2 | BS-20L-1 | BS-20L-2 |
Cavity Pitch | Variable | Variable | Variable | Variable |
Cavity Quantity | 2 | 2 | 1 | 2 |
Max Bottle Volume | 5L | 12L | 20L | 20L |
Neck Size | 60mm | 80mm | 80mm | 80mm |
Max Bottle Diameter | 200mm | 210mm | 290mm | 290mm |
Max Bottle Height | 350mm | 430mm | 480mm | 480mm |
Max Heating Power | 66KW | 70KW | 53KW | 80KW |
Install Power | 68KW | 74KW | 55KW | 86KW |
Blowing Pressure | 2.5-4.0Mpa | 2.5-4.0Mpa | 2.5-4.0Mpa | 2.5-4.0Mpa |
Main Machine Dimension | 3.5*2.2*2.4m | 5.0*1.8*2.0mm | 3.7*1.5*2.1m | 5.0*1.8*2.1m |
Preform Unscrambler Dimension | 1.1*0.8*2.8m | 1.4*0.8*2.5m | 1.4*0.8*2.5m | 1.4*0.8*2.5m |
Auto Loader DImension | 1.16*2.4*2.83m | 1.5*3.0*3.5m | 1.5*3.0*3.5m | 1.5*3.0*3.5m |
Machine Weight | 4000KGS | 5000KGS | 4000KGS | 5000KGS |
Electric Configuration
PLC | Mitsubishi |
Touch Screen | Mitsubishi |
Proximity Sensor | Autonics |
Gear Motor | ECERGEAR |
Sealing Cylinder | Airtac |
Clamping Cylinder | SMC |
Rotary Cylinder | SMC |
Transfer Motor | Xinjie |
Preform Feeding Motor | Xinjie |
High Pressure Valves | Parker |
Low Pressure Valves | Festo |
Magnetic Sensor | Airtac |
Contactor | Schneider |
Machine Introduction&Features
This large bottle servo automatic blow molding machine is its ability to produce large bottles of varying shapes and sizes, up to a maximum of 20liters. This is made possible through its unique pitch-changing structure, which allows preforms to be closely arranged during the heating process and then expanded when entering the blow mold. This design not only saves energy but also reduces the size of the machine and shortens the oven length.
The blowing machine features precise and stable servo control for clamping, ensuring quiet and smooth operation.
Its unique pitch-changing structure allows preforms to be closely arranged during heating and then expanded when entering the blow mold, resulting in a more compact machine with a shorter oven and greater energy efficiency.
An optional air recycle system further reduces compressor usage and energy consumption by recycling high-pressure air as a low-pressure air resource.
The machine is easy to install and operate.
Our Equipment Usage
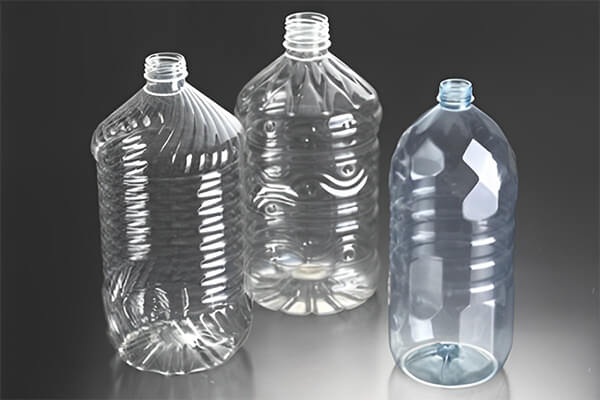
Product Details
Name | Description | |
---|---|---|
![]() |
Perform Feeding System | Servo motors are used to separate the preform, effectively solving the problem of wear between the stuck and blown preforms. |
![]() |
Preform Transfer System | The horizontal movement of the blown bottle system is driven by a servo motor, which can achieve twice the speed of the cylinder push mode, making it more precise and faster. |
![]() |
Mold Clamping System | The reaction time can be shortened to 50% of the traditional pneumatic drive, with a simple structure, no wear, and an extended service life. |
![]() |
Constant Temperature Oven | Our efficient constant temperature oven uses advanced infrared lamps, individually controlled layers, intelligent temperature control, self-rotation for even heating, and neck cooling with recycling water to prevent deformation. |
FAQs
The process starts by melting plastic resin and then injecting it into a mold. Once the plastic has cooled and solidified, a hollow tube called a parison is formed. The parison is then clamped into a mold and air is blown into it, causing it to expand and take on the shape of the mold.
There are several types of blow molding machines, including extrusion blow molding machines, injection blow molding machines, and stretch blow molding machines.
Yes, our engineer will provide free design for your checking before make the final quotation.
Lead time varies depending on the specific machine and production schedule, but typically takes 6-8 weeks.
We accept a variety of payment methods, including wire transfer, credit card, and PayPal.
We offer online technical support and troubleshooting services for the lifetime of our machines, as well as parts and service support.
Yes, we provide free online training for machine operation and maintenance to ensure our customers can use and maintain machines effectively.
We offer a 1-year warranty for all of our machines, with additional warranties available upon request.
Get Your Free Quote Now!