Automatic plastic bag labeling machine
Paging adhesive labeling machines are capable of applying labels at a faster rate than manual labeling methods, which can save time and increase productivity.
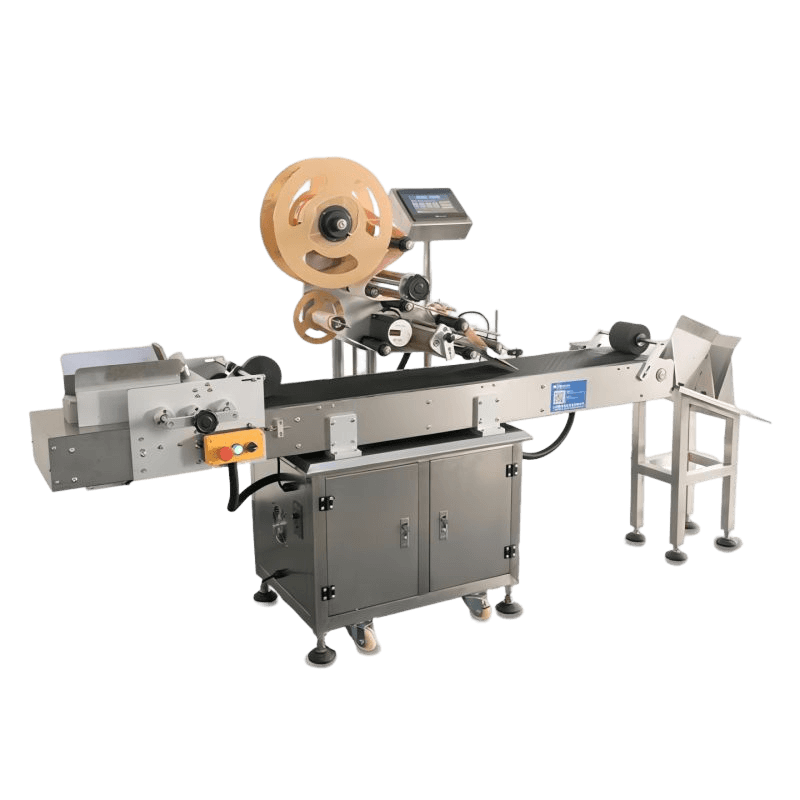
Technical Parameter
Model | BGJ-F300 |
Labeling speed | 40-60pcs/min |
Labeling material | Self-adhesive sticker, opaque or transparent label |
Applicable bag size | L:40-300mm,W:60-260mm,Height:0-2mm |
Applicable label size | L:10-80mm,W:10-80mm |
Labeling precision | +/-1mm(exclude the product and label deviation) |
Power supply | 220V 50HZ |
Overall dimension | L750mm×W580mm×H1450mm |
Weight | 250Kg |
Electric Configuration
PLC | FX3sA-30MT/Mitsubishi |
Touch Screen | TK6070iP/Weinview |
Sensor | D10BFP/Banner |
Labeling Motor | 2S86Q-030B8/KINCO |
Labeling Motor Drive | 2M860/KINCO |
Converyor Motor | D63B14-0.18KW+FB/Li-ming |
Frequency converter | S800-2S0.4G/SAVCH |
Emergency Stop | XB2-BS542/Omron |
Relay | LY2N-J 24VDC/Omron |
Machine Introduction&Features
The fully automatic paging labeling machine is suitable for automatic separation, labeling, and collection of various card products. It adopts advanced flexible card separation technology, which can smoothly separate cards without scratching the product. It is suitable for various products such as scratch cards, unfinished paper boxes, PE bags, paper bags, magazine covers, color pages, etc. In addition, the machine can also be used for applying protective films on various plastic surfaces, with high precision and no bubbles during film application.
Printing and packaging, catering industry, retail industry, daily chemical industry, clothing industry, optical industry, electronic technology, office stationery, plastic hardware.
Plastic bags,cards,tags,flat box,paper etc.
Automatically separating and feeding bags on to the conveyor for labeling.
The main materials of the equipment are stainless steel and high-grade aluminum alloy, with a solid and elegant overall structure,simple operation and maintenance.
The equipment is customized according to customer samples, with a labeling accuracy of +1mm, which can be adjusted within the technical specifications.
The structure is small and occupies a small area, which is convenient for equipment movement and placement. The equipment includes positioning devices, fault alarm production counting and an optional printing functions, etc.
Product Gallery
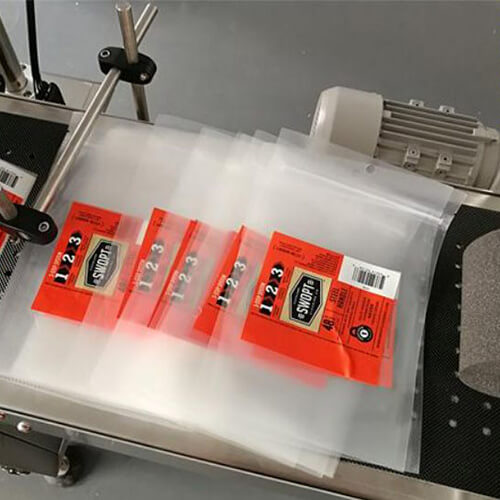
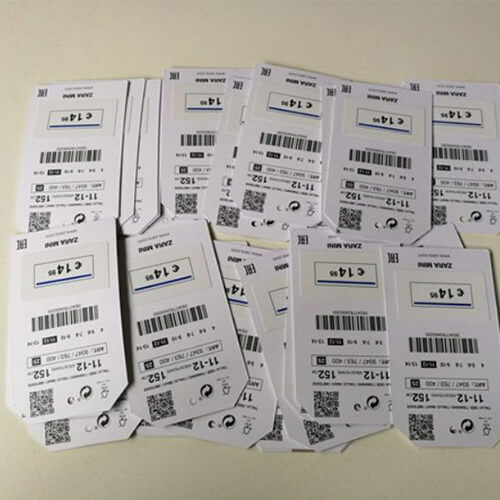
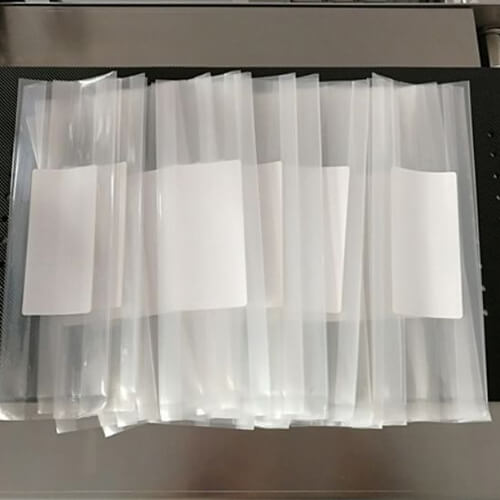
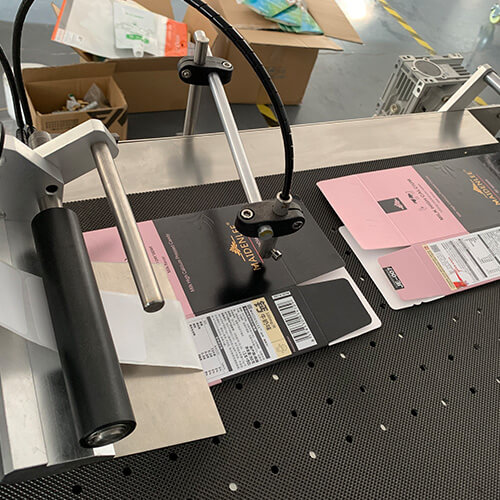
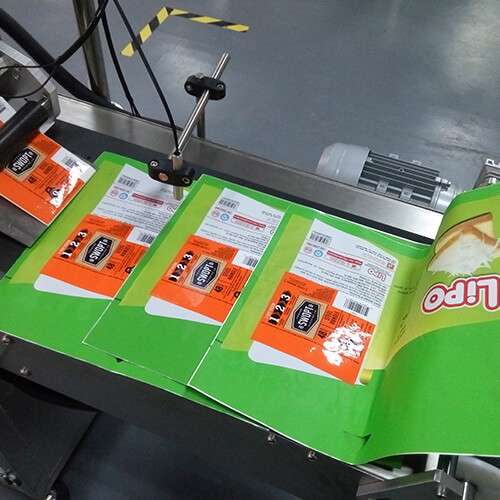
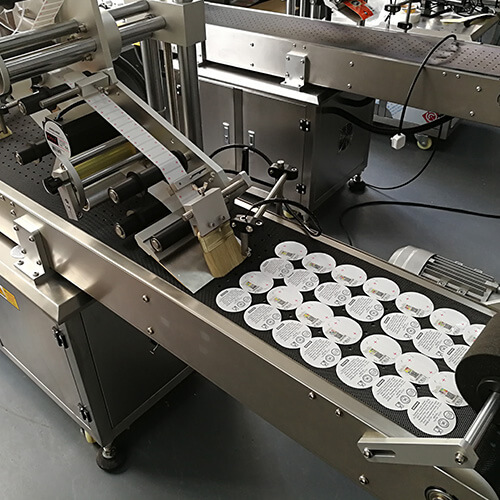
Product Details
Name | Description | |
---|---|---|
![]() |
Automatic Material Separation System | It is designed to separate bags or other flexible packaging materials from a stack or pile and feed them into a labeling machine for labeling. The system typically uses sensors, conveyors, and other mechanisms to detect and separate individual bags, ensuring that they are properly aligned and positioned for labeling. |
![]() |
Material Collecting Device | It is a type of equipment that is used after labeling to collect and organize labeled products, containers, or packages. It includes a conveyor belt, chute, or other mechanism for transporting labeled products to a designated collection area,such as a pallet. |
![]() |
Label Roll Holder | The Label Roll Holder features a spindle or mandrel that is adjustable to accommodate different label roll sizes and widths. It is also designed to minimize tension and prevent the labels from wrinkling or jamming during the dispensing process. |
![]() |
Labeling Head | The labeling head refers to the specific part of a labeling machine that applies labels onto products or packages. It is the core component of the labeling machine responsible for the actual application of labels. |
![]() |
Touch Screen | The touch screen of a labeling machine is an interface that allows the machine operator to interact with and control the labeling process. It serves as the primary user interface, providing an intuitive and convenient way to set up, monitor, and manage the labeling operations. |
![]() |
Electrical Control Cabinet | It is a crucial component that houses all the electrical and electronic components responsible for controlling and managing the machine's operations. It serves as the nerve center of the labeling machine, providing a centralized location for the electrical wiring, control circuitry, and various devices necessary for the machine to function properly. Ensures that all electrical connections are organized, protected, and easily accessible for maintenance and troubleshooting purposes. |
FAQs
Yes,our engineer will provide free design for your checking before make the final quotation.
Lead time varies depending on the specific machine and production schedule, but typically takes 6-8 weeks.
We accept a variety of payment methods, including wire transfer, credit card, and PayPal.
We offer online technical support and troubleshooting services for the lifetime of our machines, as well as parts and service support.
Yes, we provide free online training for machine operation and maintenance to ensure our customers can use and maintain machines effectively.
We offer a 1-year warranty for all of our machines, with additional warranties available upon request.
Get Your Free Quote Now!