Carbonated Drink Filling Machine
This machine is mainly used for filling carbonated beverages. It combines three functions into one unit: rinsing, filling, and capping, making the entire process automated. It can fill carbonated drinks in both PET and plastic bottles. carbonated filling machine is a state-of-the-art filling machine that meets the needs of the modern beverage industry
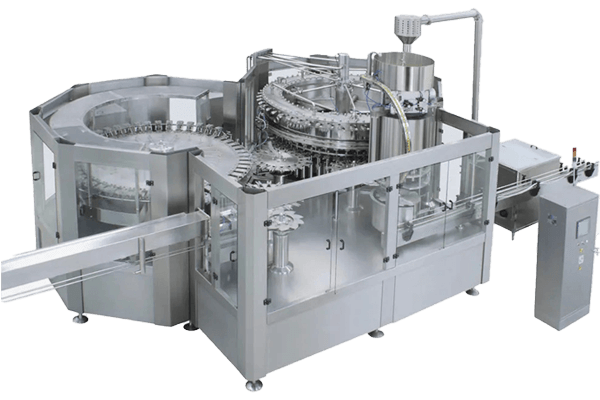
Technical Parameter
Model | PGF-18-18-6 | PGF24-24-8 | PGF32-32-10 | PGF40-40-12 |
Capacity | 6000BPH | 8000BPH | 12000BPH | 15000BPH |
Air Pressure | 0.9Mpa | 0.9Mpa | 0.9Mpa | 0.9Mpa |
Air Consumption | 0.8m3/min | 1.2m3/min | 1.2m3/min | 1.5m3/min |
Working Location | rinse 18 filler 18 capper 6 | rinse 24 filler 24 capper 8 | rinse 32 filler 32 capper 10 | rinse 40 filler 40 capper 12 |
Voltage | 380V | 380V | 380V | 380V |
Filling Method | isobaric filling | isobaric filling | isobaric filling | isobaric filling |
Machine Dimension | L2300*W1680*H2100mm³ | L3500*W2300*H2550mm³ | L3550*W2650*H2700mm³ | L4360*W3300*H2700mm³ |
Weight | 3500KGS | 5500KGS | 6000KGS | 6800KGS |
Electric Configuration
PLC | Mitsubishi |
Touch Screen | Mitsubishi |
Frequency Converter | Mitsubishi |
Motor | Taian |
Contactor | Schneider |
Hot Relay | Schneider |
Approaching Switch | Schneider |
Photoeletric Switch | Autonics |
Pneumatic Components | Airtac |
Machine Introduction&Features
Carbonated drink filler machine is a versatile filling machine integrator designed specifically for gassy beverages. This advanced filling machine can perform multiple functions, including washing, filling, and capping. It has been developed using the latest technology, which meets the strict requirements for filling gassy beverages.Carbonated filling machine is widely used in the beverage industry, especially for filling plastic caps with soda, cola, champagne, and mineral water. It is an ideal choice for large or medium-sized beverage factories due to its optimal configuration, ease of operation, reliability, and simple maintenance..
Compact design, attractive appearance, easy operation, high automation, and low labor intensity.
Uses the bottleneck blocking technology for conveying bottles, eliminating the need to adjust equipment height when changing bottle types. Corresponding nylon elements (such as arc slipper guide, thumb wheel, etc.) can be exchanged based on the bottle diameter.
Specifically designed stainless steel bottle grips are solid and durable, and avoid touching the phialine thread position to prevent secondary pollution.
Food-grade stainless steel is used for all parts in direct contact with materials, without dead angles, making cleaning easy.
Pneumatically actuated butterfly valve is used to control the inlet flow rate of liquids, ensuring accurate filling and slight turbulence in the solution barrel
High filling speed and mass flow rate, with precise filling valve and accurate control of liquids level without loss.
Features a perfect CIP control loop, program, and on-site cleaning devices.
Efficient cap settling system with perfect cap feeding and protection device.
Spiral descent mode is used for the support plate of the bottle's bottom at the outlet thumb wheel, eliminating the need to adjust the input height when changing bottle models.
Features a perfect protection system against overloading to protect facilities and operators efficiently
Air control components are also well-known imported products.
Product Details
Name | Description | |
---|---|---|
![]() |
Washing Part | The washing section of the filling machine responsible for washing bottles is a rotary bottle washing. It is primarily used for rinsing new bottles for beverages and drinking water. The main structure of the equipment that comes into contact with the rinsing medium and the external cover is made of stainless steel, including the stainless steel clamps. The machine has a simple structure that is easy to adjust, and the contact area with the bottle neck is minimal, reducing the risk of secondary pollution. Furthermore, the machine has a water collection tray to recycle the rinsing water. |
![]() |
Filling Part | The filling section is responsible for filling the material into the washed bottles provided by the bottle washing machine, using a pressure filling and negative pressure reflux method. This filling method is quick and responsive, and provides high precision filling. The filling valve has no spring, so the material does not come into contact with the spring and can be easily cleaned. To ensure the filling process and to address filling issues, the filling valve is designed to maintain a slight backflow of material when there is no bottle present or when the machine is stopped. The filling cylinder adopts a full-cylinder filling method to ensure the stability of pressure inside the cylinder. |
![]() |
Capping Part | The capping section is powered by a reduction gearbox which drives the turntable to rotate, causing the caps to be expelled from the hopper by the centrifugal force. A positive and negative cap separation device is situated at the outlet. If a negative cap is detected, it is automatically blown back into the hopper by an air current. Only positive caps can enter the chute and be conveyed to the cap feeding tray. The number of caps in the hopper is detected by photoelectric switches which control the cap conveyor and ensure that capping is performed effectively. To prevent accidents, an anti-reverse mechanism is installed on the chute, and a pair of photoelectric switches are positioned to stop the machine immediately if no cap is detected. |
FAQs
Our filling machines are designed to fill various types of beverages including carbonated and non-carbonated soft drinks, juice, tea, water, and sports drinks.
Our filling machines have a production capacity are depending on the products.
Yes, our filling machines are capable of filling different bottle sizes and shapes, including PET, glass, and aluminum cans.
Our filling machines can handle a minimum fill volume of 50ml and a maximum fill volume of 5 liters.
Yes,our engineer will provide free design for your checking before make the final quotation.
Lead time varies depending on the specific machine and production schedule, but typically takes 6-8 weeks.
We accept a variety of payment methods, including wire transfer, credit card, and PayPal.
We offer online technical support and troubleshooting services for the lifetime of our machines, as well as parts and service support.
Yes, we provide free online training for machine operation and maintenance to ensure our customers can use and maintain machines effectively.
We offer a 1-year warranty for all of our machines, with additional warranties available upon request.
Get Your Free Quote Now!