Are you struggling with the complexities of blow molding?
Now, you no longer have to worry. This blog post will take you through the intricate details of blow molding to give you a clearer picture of blow molding.
Moreover, Packerasia is a leading manufacturer of blow molding machines in China. Our team can also help you find the best machine for your needs.
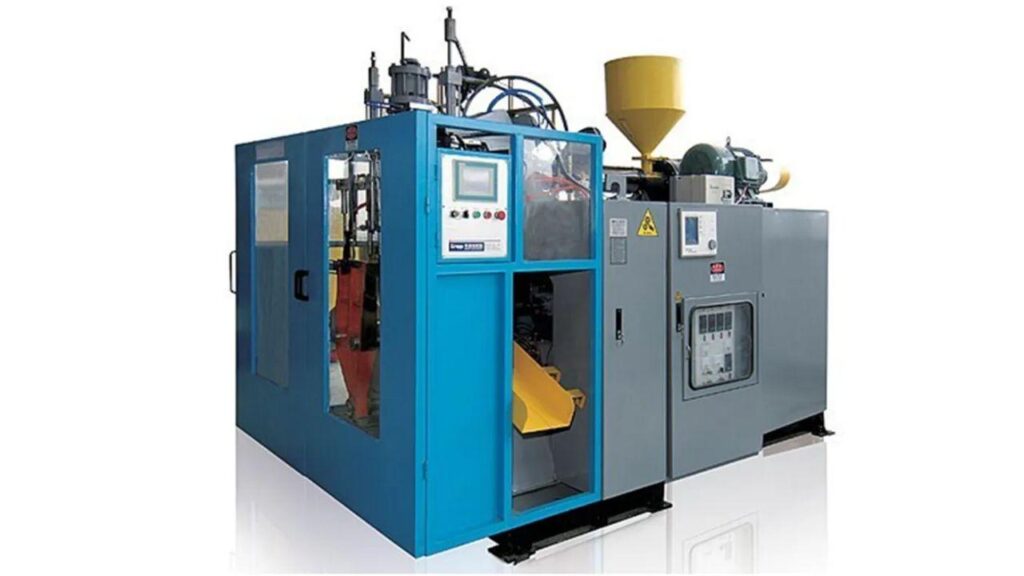
What is Extrusion Blow Molding?
Extrusion Blow Molding is a highly versatile and widely used manufacturing process in the plastics industry.
It involves transforming plastic resins into hollow and seamless products, such as bottles, containers, toys, and automotive components.
The process is known for its efficiency in mass production and its ability to create lightweight yet durable products.
The Extrusion Blow Molding Process
The Extrusion Blow Molding process consists of several essential steps that enable the production of hollow plastic items.
First, plastic resin pellets are fed into an extruder, where they are melted to form a molten plastic mass. The extruder then shapes the molten plastic into a hollow tube, known as a “parison.”
Next, the parison is transferred to a mold, and compressed air is blown into it, causing it to expand and take the shape of the mold’s cavity. After cooling and solidification, the plastic product is ejected from the mold.
Finally, finishing touches such as trimming off excess plastic and adding details are performed to achieve the desired final product.
Key Terms Used in the Extrusion Blow Molding Process
Understanding key terms used in Extrusion Blow Molding is crucial for grasping the intricacies of the process:
Extruder: The machine responsible for melting the plastic resin and shaping it into a parison.
Parison: The hollow tube-like structure formed by the extruder, which serves as the precursor to the final product.
Mold: The cavity that imparts the desired shape to the molten plastic during the blowing stage.
Inflation: The step where compressed air is blown into the parison, expanding it against the mold walls and shaping it.
Materials Used in Extrusion Blow Molding
Several types of plastic resins are commonly used in Extrusion Blow Molding due to their unique properties and versatility:
Polyethylene (PE): This resin comes in different forms, such as high-density polyethylene (HDPE) and low-density polyethylene (LDPE). HDPE offers excellent rigidity and strength, making it ideal for containers, while LDPE provides flexibility suitable for squeeze bottles and toys.
Polypropylene (PP): Known for its high chemical resistance and toughness, PP is often used to produce containers for household chemicals, food, and beverages.
Polyethylene Terephthalate (PET): PET is widely used in the production of clear plastic bottles for beverages and personal care products due to its excellent clarity, strength, and barrier properties.
Polyvinyl Chloride (PVC): PVC is a durable and weather-resistant resin often used for creating pipes, tubes, and automotive components.
Why Resins Are Suitable for Extrusion Blow Molding
The chosen resins offer distinct advantages that make them well-suited for the Extrusion Blow Molding process:
PE: Its ability to withstand impact and its resistance to chemicals make it ideal for products that require durability and strength. The flexibility of LDPE is beneficial for applications where squeezability is desirable.
PP: Its chemical resistance and toughness ensure the safe containment of various substances, making it a popular choice for a wide range of packaging needs.
PET: Its exceptional clarity, strength, and ability to resist gas and moisture transmission make it perfect for creating transparent bottles used in the food and beverage industry.
PVC: Its weather resistance and durability make it an excellent choice for outdoor and automotive applications where exposure to the elements is a concern.
The Extrusion Blow Molding Process
The Extrusion Blow Molding process can be broken down into several essential stages, each contributing to the successful creation of hollow plastic products:
Extrusion of a Tube or Parison
In this initial step, plastic resin pellets are fed into the extruder’s hopper.
Inside the extruder, the resin is heated and melted to form a uniform molten mass.
The molten plastic is then forced through a die, which shapes it into a hollow tube known as the parison.
Inflation of the Parison Against the Mold Walls
The parison, still in a molten state, is transferred to the mold, which is shaped to match the desired final product.
The mold is closed around the parison, and compressed air is blown into it.
As a result, the parison expands and takes the shape of the mold cavity, forming the product’s outer geometry.
Cooling and Solidification of the Plastic
Once the molten plastic has taken the mold’s shape, it is left to cool and solidify.
Cooling is typically achieved by circulating water or air around the mold,
which rapidly reduces the plastic’s temperature, enabling it to solidify and maintain the desired shape.
Ejection of the Part from the Mold
After the plastic has solidified and reached the appropriate level of rigidity, the mold opens, and the finished product is ejected from the mold cavity.
The cycle then repeats for the production of the next part.
Deflashing and Finishing of the Part
Upon ejection, the plastic part may have excess material, known as flash, which is trimmed off to achieve the final desired dimensions.
Additional finishing processes, such as printing, labeling, or assembling, can be performed to enhance the product’s appearance and functionality.
the Process of Compression Molding and Insert Molding
While Extrusion Blow Molding is the primary process used, variations such as compression molding and insert molding are worth mentioning:
Compression Molding:
Compression Molding is a supplementary technique that involves pre-forming the plastic resin into a specific shape before it enters the Extrusion Blow Molding process.
The pre-formed plastic is then placed into the mold, and the blowing process completes the final shaping.
Insert Molding:
Insert Molding is another variation where pre-formed components, such as metal inserts or other plastic parts, are placed inside the mold before the Extrusion Blow Molding process begins.
The molten plastic flows around these inserts, creating a composite product with integrated parts.
Types of Extrusion Blow Molding Processes
The types of extrusion process are as follows:
Shuttle Extrusion Blow Molding
Shuttle Extrusion Blow Molding is a method that utilizes machines equipped with two molds, often referred to as “shuttles.”
The shuttle system allows for continuous production, since while one mold is in use, the other can be loaded with a new parison and prepared for the next cycle.
This setup significantly reduces downtime between cycles and increases overall productivity.
Shuttle machines are particularly suitable for the production of smaller and medium-sized products, where short cycle times and high output are essential.
Their flexibility in accommodating different mold sizes and shapes makes them a preferred choice for manufacturers with varied production requirements.
Blow Direct Screw (BDS) Extrusion Blow Molding
Blow Direct Screw (BDS) Extrusion Blow Molding is a more streamlined process compared to traditional methods.
In BDS machines, the plasticizing screw used in the extruder also serves as the blowing pin, eliminating the need for a separate blowing pin. This integration reduces cycle times and simplifies the overall process.
BDS machines excel in high-volume production of smaller products with consistent wall thickness and precise dimensions. The elimination of the blowing pin reduces maintenance requirements and allows for increased production efficiency.
Products Produced with Extrusion Blow Molding
Extrusion Blow Molding is a versatile process widely used to create a broad range of products.
The process’s ability to produce hollow and seamless structures makes it ideal for various applications, including packaging, automotive, household, and industrial products.
Some common products manufactured using Extrusion Blow Molding include:
Plastic bottles for beverages, cleaning agents, and personal care products.
Containers for food storage, pharmaceuticals, and industrial chemicals.
Automotive components such as fuel tanks, ducts, and fluid reservoirs.
Toys, play equipment, and recreational items.
Household items like buckets, jugs, and containers.
Advantages of Extrusion Blow Molding
Extrusion Blow Molding has the following advantages:
Cost-effectiveness for High Volume Production
Extrusion Blow Molding is highly efficient in mass production, allowing for the creation of large quantities of identical products in a short time. This scalability leads to reduced production costs per unit.
High Strength-to-Weight Ratio
The hollow structure of Extrusion Blow Molded products results in lightweight yet robust items. This combination of strength and reduced weight contributes to cost savings in materials and transportation.
Design Flexibility
Extrusion Blow Molding offers extensive design possibilities, enabling the creation of complex shapes and intricate details. Manufacturers can customize products to meet specific requirements and branding preferences.
Insulation and Acoustical Properties
The hollow nature of Extrusion Blow Molded products provides natural insulation, making them suitable for thermal and acoustic applications. This feature is especially beneficial in automotive components and building materials.
How Can We Help You?
Packerasia is a leading manufacturer of labeling and packaging machines in China. Our team can help you find the best machine for your needs. We can modify existing lines to suit your project.
Please feel free to contact us to discuss your customization requirements, or you can click here to view our range of blow molding machines.
FAQs
What is Extrusion Blow Molding?
Extrusion Blow Molding is a manufacturing process used to create hollow plastic products. It involves melting plastic resins, shaping them into a hollow tube (parison) using an extruder, and then inflating the parison against a mold to form the final product.
What are the common materials used in Extrusion Blow Molding?
Common materials used in Extrusion Blow Molding include Polythylene (PE), Polypropylene (PP), Polyethylene Terephthalate (PET), and Polyvinyl Chloride (PVC). These materials offer various properties, making them suitable for different applications.
What products can be made with Extrusion Blow Molding?
Extrusion Blow Molding is used to produce a wide range of products, such as plastic bottles, containers, automotive components, toys, and household items.
What is the Extrusion Blow Molding process?
The Extrusion Blow Molding process involves several steps: extruding a parison, inflating the parison against the mold walls, cooling and solidifying the plastic, ejecting the part from the mold, and finishing the product.
What are the advantages of Extrusion Blow Molding?
The advantages of Extrusion Blow Molding include cost-effectiveness for high volume production, a high strength-to-weight ratio, design flexibility, and inherent insulation and acoustical properties.
What types of Extrusion Blow Molding processes are there?
There are two main types: Shuttle Extrusion Blow Molding, which uses machines with two molds for continuous production, and Blow Direct Screw (BDS) Extrusion Blow Molding, where the plasticizing screw also serves as the blowing pin.
Which products are suitable for Shuttle Extrusion Blow Molding?
Shuttle Extrusion Blow Molding is ideal for producing smaller and medium-sized products with moderate production volumes due to its ability to minimize downtime and increase productivity.
What are the capabilities of Blow Direct Screw (BDS) Extrusion Blow Molding?
BDS Extrusion Blow Molding is well-suited for high-volume production of smaller products with consistent wall thickness and precise dimensions.
Are there any finishing processes required after Extrusion Blow Molding?
Yes, after the product is ejected from the mold, it may undergo deflashing to remove excess material. Additional finishing processes like printing and labeling can be performed to enhance the product’s appearance.
How important is Extrusion Blow Molding in modern manufacturing?
Extrusion Blow Molding plays a significant role in the production of various everyday products, and its efficiency and versatility have made it an essential process in modern manufacturing.
What can we expect in the future for Extrusion Blow Molding technology?
As technology advances, we can anticipate further improvements in Extrusion Blow Molding, such as better materials, machinery, and process optimization, leading to expanded applications and more efficient production methods.