Choosing the right blow molding machine can be a daunting task. With a multitude of options available in the market, each with its unique features and specifications, it’s easy to feel overwhelmed. You might be grappling with questions about the machine’s compatibility with your production requirements, its energy efficiency, or even its cost-effectiveness.
At Packerasia.com, we understand these challenges. That’s why we’ve put together this comprehensive guide to help you navigate through the selection process. Our aim is to equip you with the knowledge you need to make an informed decision that aligns with your business needs and budget.
In this guide, we’ll delve into the key factors you need to consider when choosing a blow molding machine, from understanding different types of machines to evaluating their features and benefits. So, let’s embark on this journey to find the perfect blow molding machine for your operations.
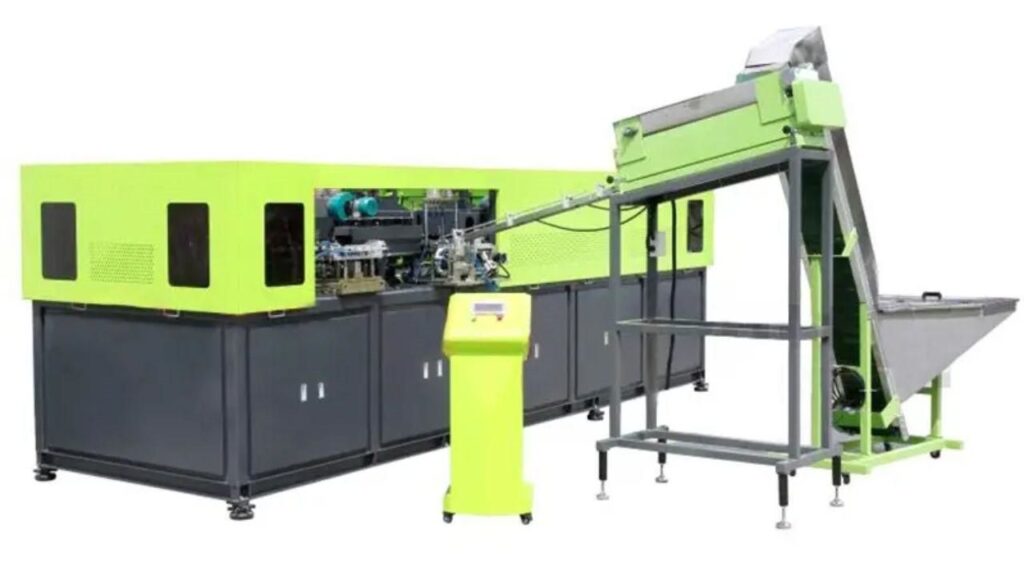
What is a Blow Molding Machine?
Blow molding is a method for making empty plastic items out of flexible materials. In this process, plastic tubes called type blanks or preforms are heated and blown up.
The comparison is put between two forms that have the shape of the product that is wanted. The tube is then filled with air to make it bigger, which makes the walls thinner and more like the shape of the mold.
After the blow molding process is done, the product is cooled, pushed out, cut, and set up for the next step.
What are the features of blow molding machines
The following are the most important features of blow molding tools:
Control system
Most modern tools have easy-to-use, high-precision control systems. These systems may have touch screen monitors, programmable logic controllers (PLCs), and software for tracking and controlling the process.
Die Heads
The form and size of the result depends on the die head. Some tools have more than one die head, allowing multiple parts to be produced at the same time.
Clamping Systems
Strong clamping force maintains process quality and uniformity. Choose tools with hydraulic or electric clamping systems that give you precise control and a strong grip.
Extruders
Before molding, plastics are heated and mixed in an extruder. Choose an extruder with uniform heating and high plasticizing capacity.
Types of Blow Molding Machines
Blow molding machines come in three main types:
Extrusion blow molding machines:
These machines are great for making big, high-volume items like water tanks and plastic buckets. They work by pushing out a long tube of plastic, which is then cut and blown up in a mould.
Injection blow molding machines:
Injection blow molding machines are used to make things like pill bottles that are smaller and more accurate. They work by pouring liquid plastic into a mould to make a pre-shaped part, which is then expanded to its final shape.
Stretch blow molding machines:
These machines are used to make high-quality cases with clear glass, like those for fizzy drinks. During the expansion process, the mould is stretched, which aligns the molecules of the plastic to make the container stronger and clearer.
Each type of machine has its own benefits, so it’s important to choose the right one for the product and production needs.
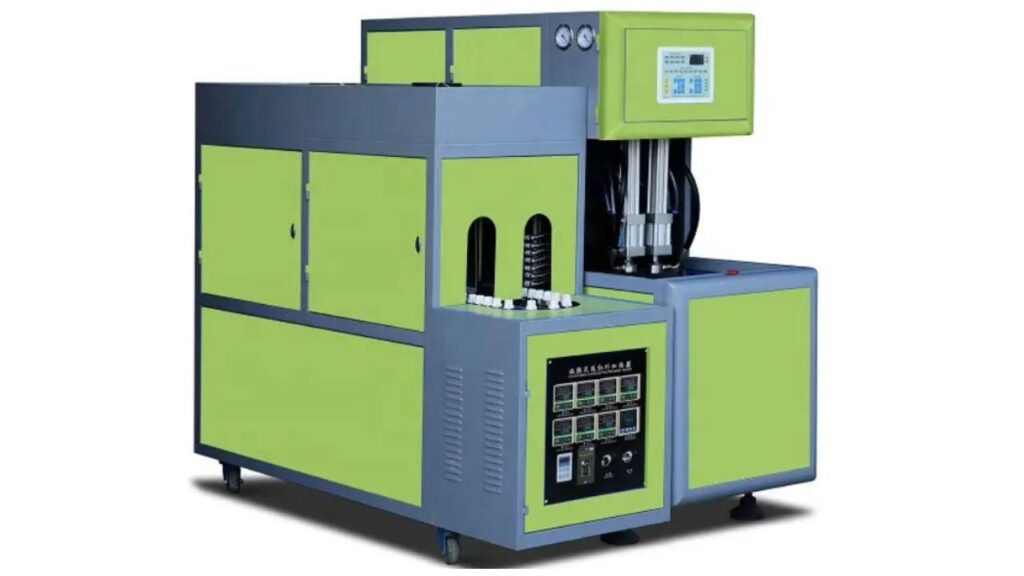
Looking for a Blow Molding Machine?
You surely know that picking the right blow molding machine is crucial to the success of your line.
But do you know what some of the most important things to think about are?
Type of product to be made:
The type of machine you need will depend on how the product is made and how complicated it is. For example, if you are making complicated parts with multiple layers, you may need a machine that can co-extrusion.
Production Needs:
Think about your speed and output. For a machine to have a higher output, it may need to have faster cycle times or more holes. Also think about your output plan. Do you need a machine to run all the time or in batches?
Compatibility with materials:
Not all tools can work with all kinds of plastics. Make sure your machine can handle the material you want to use, whether it’s HDPE, LDPE, PP, PVC, or PET.
Energy efficiency:
Machines that use less energy and are better for the world cost less and use less energy. Look for machines with things like servo-driven motors or modern heating systems that use less energy.
Size and Space Needs of the Machine:
Make sure your building has enough room for the machine and how it works. Also, think about how heavy the machine is and if your tools can handle it.
Budget and cost-effectiveness:
Think about both how much the machine will cost up front and how much it will cost to run and maintain over time. A cheaper machine may cost more in the long run if it doesn’t work well or needs to be fixed often.
FAQs
What is a blow molding machine?
A blow molding machine is a manufacturing device used to produce hollow plastic parts by inflating a heated plastic tube until it forms into the shape of the machine’s cavity.
What are the different types of blow molding machines?
There are three main types of blow molding machines: extrusion blow molding machines, injection blow molding machines, and stretch blow molding machines. Each type is suited to different kinds of products and production needs.
What factors should I consider when choosing a blow molding machine?
Key factors to consider include the type of product to be produced, production requirements, material compatibility, energy efficiency, machine size and space requirements, and budget and cost-effectiveness.
What are some key features of blow molding machines?
Key features to look for in a blow molding machine include control systems, die heads, clamping systems, and extruders.
Why is maintenance and after-sales support important for blow molding machines?
Regular maintenance is crucial to keep your machine running smoothly and efficiently. Good after-sales support, including the availability of spare parts and technical support, can save you time and money in the long run.
What are some examples of products made by blow molding machines?
Blow molding machines are used to produce a wide range of plastic containers and other hollow parts, including water bottles, pharmaceutical bottles, plastic drums, and automotive parts.
What is the production capacity of a blow molding machine?
The production capacity of a blow molding machine can vary widely depending on the type of machine and the specific model. Some machines can produce up to 1200 bottles per minute for small single-serve bottles, and up to 400 bottles per minute for larger handleware bottles.
What materials can be used in a blow molding machine?
Blow molding machines can handle a variety of plastic materials, including HDPE, LDPE, PP, PVC, and PET. However, not all machines are compatible with every type of plastic, so it’s important to ensure your machine can handle your chosen material.
What is the energy efficiency of a blow molding machine?
The energy efficiency of a blow molding machine can vary depending on the specific model and its features. Some machines have energy-saving features such as servo-driven motors or advanced heating systems.
What is the cost of a blow molding machine?
The cost of a blow molding machine can vary widely depending on the type of machine, its features, and the manufacturer. It’s important to consider both the upfront cost of the machine and the long-term costs of operation and maintenance.
Need a new cartoning machine?
This is how to buy a blow molding machine. If you are planning to buy a new blow molding machine and need more expert advice, contact us today! Packerasia understands which machine will perfectly meet your product requirements and business goals.