Each plastic component necessitates a tailored manufacturing process, which can vary significantly from one product to another. Injection molding is employed for producing solid components, whereas blow molding is utilized for fabricating plastic items with hollow sections, such as bottles and containers.
Injection stretch blow molding integrates the processes of injection molding and blow molding. Initially, plastic is molded into a solid preform, crafting a threaded bottle neck. After the preform cools, it enters a stretch blow mold machine. Subsequently, the preform undergoes reheating via an infrared heater and is transformed into a plastic bottle through forced compressed air.
Injection molding and blow molding constitute pivotal processes in the realm of plastic manufacturing. The resulting products find applications across diverse industries such as automotive, food service packaging, electronics, medical devices, irrigation, dental, firearms, as well as the energy and environmental sectors.
To enhance your comprehension of the various manufacturing methodologies applicable to your project, we have assembled an overview elucidating the primary types of injection and blow molding techniques employed by plastics manufacturers.
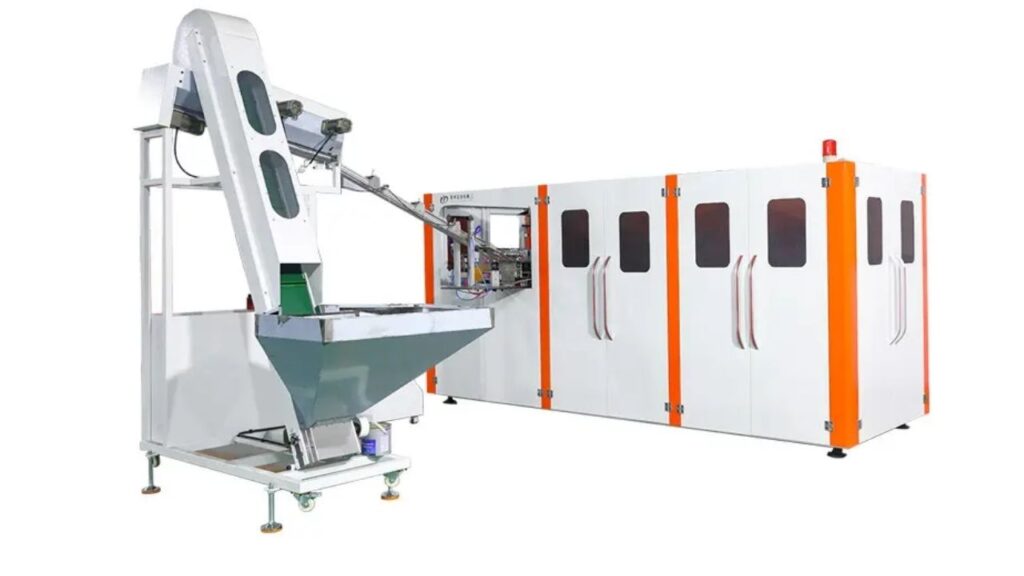
The Injection Molding Process
Injection molding is a versatile manufacturing method used to produce plastic products in high volume. It involves injecting molten plastic material into a mold cavity to shape the desired product. There are different types of injection molding methods, each with unique advantages.
The injection molding process begins with the preparation of plastic resin pellets, which are fed into a hopper. The pellets are then heated and melted inside the barrel of an injection molding machine.
Once the material is in a molten state, it is injected into the mold cavity under high pressure. The mold is kept closed until the plastic has cooled and solidified. After solidification, the mold opens, and the finished product is ejected.
Types of Injection Molding
Thermoplastic Injection Molding: This method utilizes thermoplastic polymers that can change to a liquid state when heated. It is widely used due to its efficiency and ability to produce a wide range of products. This materials can be melted, cooled, and re-melted multiple times without undergoing any significant chemical changes, making them highly recyclable.
Overmolding: In this process, an injection mold covers another substance, enhancing product performance or durability. It is commonly used for creating handles and grips on tools. Overmolding allows manufacturers to combine different materials, such as soft rubber grips over a rigid plastic tool body, resulting in a more comfortable and functional product.
Insert Molding: Insert molding involves combining two or more components into a single finished product. It is beneficial for incorporating metal parts or other materials into a plastic product. The inserts are placed into the mold before the injection process, and the molten plastic encapsulates them, creating a strong bond.
Cold Runner Injection Molding: Cold runner injection molding uses a sprue to fill the runners, which inject plastic resin into the mold cavity. This method reduces material wastage as the runner system remains at room temperature and can be reused for subsequent cycles. However, it can result in increased cycle times and may not be suitable for all applications.
Hot Runner Molds: Hot runner molds use a manifold to heat melted plastic resin and then send the material through a gate to fill the mold cavity. It results in faster production and minimal material waste compared to cold runner molding. The heated manifold keeps the plastic in a molten state throughout the process, eliminating the need for re-melting the plastic during each cycle.
The Blow Molding Process
Blow molding is a process used to create hollow plastic products. The raw plastic material is first formed into a hollow tube, known as a parison, which is then pressed into a cooled metal mold. Compressed air is then used to inflate the parison, shaping it into the final product.
The process starts with the extrusion of plastic in the form of a continuous tube called a parison. The parison is then transferred to a mold cavity, where it is clamped between two halves of the mold.
Compressed air is blown into the parison, expanding it against the mold’s inner surface to take the shape of the desired product. The plastic is then cooled and solidified in the mold before the finished product is ejected.
Types of Blow Molding
Injection Blow Molding: This method involves using a blow or core rod throughout the process. A parison is first injected into a split mold cavity around the rod and is then transferred to a blow mold machine where forced air creates the final shape.
Injection blow molding is commonly used for producing small bottles for pharmaceuticals, cosmetics, and personal care products.
Extrusion Blow Molding: Extrusion blow molding can be continuous or intermittent. In continuous extrusion blow molding, a parison is constantly fed into the mold, and each form is cut off as it forms.
In intermittent extrusion blow molding, a new plastic is expelled from the metal mold when it is cooled, and the parison is fed into the mold only after the preceding parison is expelled. Extrusion blow molding is suitable for producing a variety of products, including milk jugs, automotive ducts, and household containers.
Injection Stretch Blow Molding: Combining the injection molding and blow molding processes, this method first molds the plastic into a solid preform.
It is then reheated and blown into a plastic bottle with forced compressed air. Injection stretch blow molding is commonly used for producing PET bottles for carbonated beverages, water, and other beverages due to its ability to create lightweight and durable bottles with excellent clarity.