Blow molding is everywhere around us and you don’t even realize it. The plastic bottles you drink from are blow molded.
Blow molding has become one of the most common and widely used manufacturing processes in the plastics industry.
The popularity of the blow molding process is due to its simplicity, efficiency, and ability to produce a variety of plastic products of consistent quality.
But what exactly is plastic? And how does it work? Read on to find out!
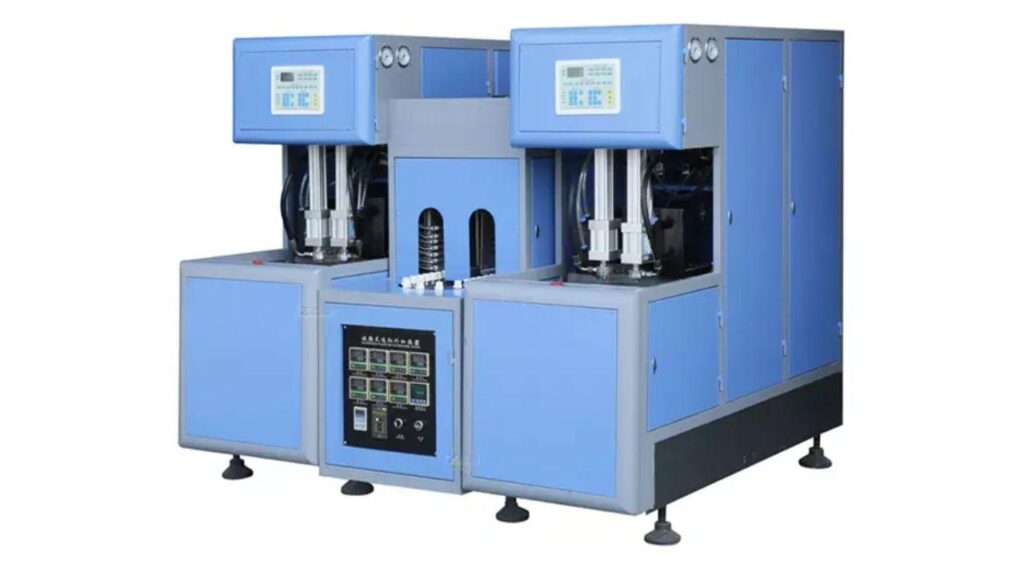
What is Blow Molding?
Blow molding is a highly versatile plastic production process that has become a cornerstone of the packaging industry.
The process starts with the melting of plastic resin pellets, which are then extruded into a tube-like form called a parison.
The parison is then clamped between two halves of a mold, and air is blown into it, expanding the plastic to take the shape of the mold’s cavity.
Once the plastic cools and solidifies, the mold opens, and the finished product is ejected.
This method allows for the efficient and rapid production of hollow objects with consistent wall thickness, making it ideal for manufacturing bottles, containers, and various other products.
In addition, a blow molding machine is a machine for blow molding. There are many types of blow molding machines.
As we introduce you to blow molding as a process, we want to help you choose the right blow molding machine for your business. Contact us today to find the right blow molding machine for you!
The History of Blow Molding
Blow molding has its origins in the art of glass blowing, a technique dating back thousands of years. Ancient artisans used their breath to shape molten glass into various forms, foreshadowing the principles of modern blow molding.
However, it wasn’t until the 1930s that the first commercial blow molding machines emerged. These machines were primarily used for creating simple plastic bottles.
With advancements in materials and technology, the process expanded to accommodate low-density polyethylene (LDPE) and high-density polyethylene (HDPE), broadening the range of products that could be produced. Today, blow molding has evolved into a sophisticated and essential industrial process.
What Can You Make with Blow Molding?
The versatility of blow molding is evident in the wide range of products it can produce.
Plastic bottles, containers, and jars for food, beverages, and household products are among the most common items manufactured through blow molding.
The automotive industry also heavily relies on blow molding to produce fuel tanks, air ducts, and various interior and exterior components.
In addition to these, blow molding finds applications in the production of toys, medical equipment, and industrial containers.
The ability to create seamless, hollow structures makes it a preferred method for manufacturing lightweight, yet robust, plastic products.
The Blow Molding Process
Blow molding encompasses several variations, each tailored to meet specific manufacturing requirements:
Extrusion Blow Molding (EBM):
This process is widely used for producing bottles. During EBM, a continuous parison is extruded through a die and then clamped into a mold where it is inflated with compressed air. The final product retains the mold’s shape and is subsequently cooled and ejected.
Injection Blow Systems (IBS):
IBS combines the principles of injection molding and blow molding. The first step involves creating a preform, which is a solid plastic piece formed by injection molding. The preform is then transferred to the blow mold, where it is reheated and blown into the desired shape.
Injection Stretch Blow Molding (ISBM):
ISBM is commonly used for high-precision products such as PET bottles. The process starts with the injection molding of a preform, which is then stretched in one direction to orient the molecules. Finally, the preform is reheated and blown into the final product’s shape.
Blow Molding Materials
Blow molding supports a wide array of plastic materials, each possessing unique properties suitable for different applications.
Polyethylene, both low and high-density (LDPE and HDPE), is popular due to its ease of processing and excellent chemical resistance.
Polypropylene (PP) is another commonly used material known for its high stiffness and heat resistance, making it suitable for products such as containers and automotive parts.
Polyvinyl chloride (PVC) is preferred for its durability and versatility, while PET (polyethylene terephthalate) is widely used for producing beverage bottles due to its excellent clarity and barrier properties.
Advantages of Blow Molding
Blow molding offers numerous advantages that make it stand out among other plastic manufacturing methods:
Cost-effectiveness:
The process minimizes material waste, reducing production costs and making it an economically viable option for mass production.
Reduced Flash:
Unlike some molding techniques that may produce excess material (flash), blow molding creates seamless products, eliminating the need for extensive trimming and minimizing material loss.
Flexibility:
Blow molding allows for the production of intricate and complex shapes with ease, providing designers and manufacturers with greater design freedom.
Contact us now!
In short, blow molding’s combination of efficiency, versatility, and cost-effectiveness has become a cornerstone of the plastics manufacturing industry.
Choosing the blow molding process to bring your product to life is an excellent solution for mass-producing simple, effective designs without breaking the bank.
We have a team of highly trained professionals who can take your product from idea to reality. Contact us today!
FAQs
What is blow molding?
Blow molding is a plastic manufacturing process that creates hollow plastic products. It involves heating plastic resin to a molten state and then shaping it into a hollow tube called a parison. The parison is placed in a mold, and compressed air is blown into it, causing the plastic to expand and take the shape of the mold’s cavity. Once cooled and solidified, the product is ejected from the mold, resulting in a finished, hollow plastic item.
What types of products can be made through blow molding?
Blow molding is incredibly versatile and can produce a wide range of products, including plastic bottles, containers, jars, automotive parts, toys, medical equipment, and industrial containers. It is commonly used in the packaging industry to manufacture bottles and containers for food, beverages, and household products. In the automotive industry, blow molding is utilized to produce fuel tanks, air ducts, and various interior and exterior components.
How does blow molding compare to other plastic manufacturing methods?
Blow molding offers several advantages over other plastic manufacturing techniques:
Cost-effectiveness: Blow molding minimizes material waste, reducing production costs and making it ideal for mass production.
Reduced Flash: Unlike some molding methods that produce excess material (flash), blow molding creates seamless products, reducing the need for extensive trimming and minimizing material loss.
Flexibility: Blow molding allows for the production of intricate and complex shapes with ease, providing designers and manufacturers with greater design freedom.
What materials are suitable for blow molding?
Blow molding supports a variety of plastic materials, each with unique properties suited for different applications. Common materials used in blow molding include:
Polyethylene (both low and high-density): Known for its chemical resistance and ease of processing.
Polypropylene: Offers high stiffness and heat resistance, making it suitable for containers and automotive parts.
Polyvinyl chloride (PVC): Known for its durability and versatility.
PET (polyethylene terephthalate): Widely used for beverage bottles due to its clarity and barrier properties.
What are the different types of blow molding?
Blow molding comes in various variations, each tailored to specific needs:
Extrusion Blow Molding (EBM): Used for producing bottles and containers by extruding a parison and inflating it in a mold.
Injection Blow Systems (IBS): Combines injection molding and blow molding to create products from a preform.
Injection Stretch Blow Molding (ISBM): Used for high-precision products, such as PET bottles, by stretching the preform before blowing it into the final shape.
How has blow molding evolved over time?
The origins of blow molding can be traced back to ancient glass blowing techniques. In the 1930s, the first commercial blow molding machines were developed, mainly used for simple plastic bottles. Over time, advancements in materials and technology allowed blow molding to expand its applications, including the production of various plastic products, and becoming an essential industrial process.
What industries benefit from blow molding?
Blow molding finds applications in multiple industries. Some of the key beneficiaries include:
Packaging industry: For the production of bottles, containers, and jars for food, beverages, and household products.
Automotive industry: For manufacturing fuel tanks, air ducts, and various interior and exterior components.
Toy industry: For creating plastic toys of different shapes and sizes.
Medical equipment industry: For producing medical containers and equipment.
How can blow molding be environmentally friendly?
Blow molding can contribute to sustainability by minimizing material waste through efficient manufacturing processes. Its ability to create seamless products reduces the need for excessive trimming, further conserving raw materials. Additionally, some blow molding materials, such as PET, are recyclable, promoting the circular economy and reducing the environmental impact of plastic production.
Can complex designs be achieved with blow molding?
Yes, blow molding offers the flexibility to produce intricate and complex shapes with ease. The process allows for the creation of products with consistent wall thickness, ensuring the structural integrity of the final design. This design freedom makes blow molding an excellent choice for custom and innovative plastic products.
How can I get started with blow molding for my product?
If you are considering blow molding for your plastic product, you can begin by contacting a reputable blow molding company. They can provide expert assistance with product design, material selection, and the manufacturing process. Collaborating with experienced professionals will ensure that your vision is transformed into a successful, high-quality plastic product.