Palletizers play a vital role in optimizing warehouse and distribution center operations by efficiently stacking and organizing products onto pallets.
However, choosing the right palletizer for your specific needs can be a daunting task. Read this blog, here, which will give you an introduction to the different types of palletizers and provide valuable advice on making an informed decision.
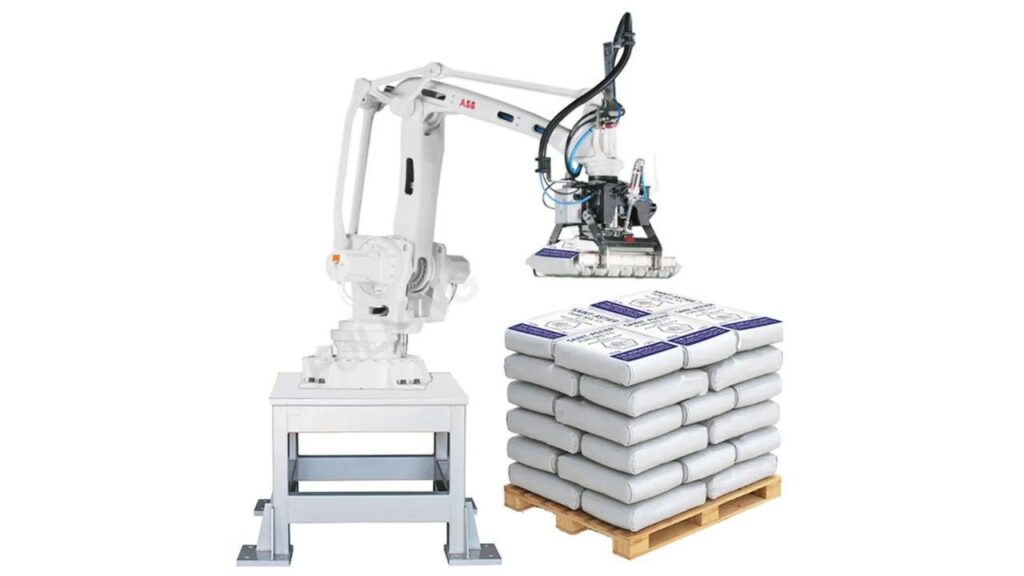
What is a palletizer?
A palletizer is a complex and valuable piece of mechanical equipment used to simplify the process of stacking and organizing products onto pallets.
It plays a key role in automating the labor-intensive task of palletizing, eliminating the need for manual operations and greatly increasing overall productivity. Palletizers help logistics and warehousing operations to run smoothly by efficiently palletizing products on pallets in a systematic manner.
The versatility of palletizers lies in their ability to meet a wide range of packaging requirements and production volumes. Manufacturers have developed a range of palletizer types, each of which meets the needs of specific industries. Understanding the different types of palletizers can help companies choose the most suitable option for their unique needs.
Types of palletizers
There are four types of palletizers:
Robot palletizers:
Among the many advanced palletizers available, robot palletizers are the pinnacle of technological advancement in the packaging industry. Equipped with state-of-the-art robotic arms and multifunctional end tools, these machines exhibit exceptional precision and flexibility in handling products.
They demonstrate their versatility by picking up, placing and stacking products onto pallets with finesse, effortlessly adapting to a wide range of product shapes, sizes and configurations.
This adaptability is particularly beneficial for industries with a wide range of products, as robot palletizers can be quickly reprogrammed to adjust palletizing patterns to ensure an efficient and seamless packaging process. The seamless integration of the robot palletizer into the production line results in unparalleled automation, minimizing manual intervention and increasing overall productivity.
High-level palletizers:
High-level palletizers are the ideal solution for industries seeking increased productivity and rapid palletizing capabilities.
These palletizers are mounted in an elevated position and receive the product from the conveyor belt, gently stacking it onto the pallet under the force of gravity.
This setup ensures smoothness and continuity in the palletizing process, making high level palletizers ideal for high speed operations.
In addition, their robust construction allows them to handle heavy loads with ease, making them ideal for businesses that handle large quantities of products.
By efficiently handling heavy loads and maintaining a steady flow of palletized goods, high-level palletizers streamline warehousing and distribution processes, improving overall efficiency and reducing operating costs.
Low-level palletizers:
While high-level palletizers are highly regarded in large-scale operations, low-level palletizers have proved their worth in smaller production lines and industries with different packaging needs. These palletizers work on the floor, laying products in a single layer before gently lifting and placing them on pallets.
Although they operate at a slightly slower speed compared to high-level palletizers, they more than make up for this with their adaptability in handling a wide range of products.
From small items to irregularly shaped packages, low-level palletizers effectively position products for shipment and storage, making them an important asset for companies wishing to streamline their material handling processes without compromising quality.
Conventional palletizers:
While robotic palletizers and advanced palletizers offer impressive versatility and speed, conventional palletizers offer a reliable, economical solution for specific applications.
These palletizers use robotic arms to carefully stack products in a predetermined pattern. While they may lack the flexibility of robots, their reliable performance is highly regarded in industries that require consistent and repetitive palletizing patterns.
Conventional palletizers are a popular choice for standardized product packaging companies because they ensure consistent and accurate stacking, reducing the risk of product damage during the palletizing process.
In addition, the cost-effectiveness of conventional palletizers makes them a practical choice for companies seeking a reliable and efficient palletizing solution.
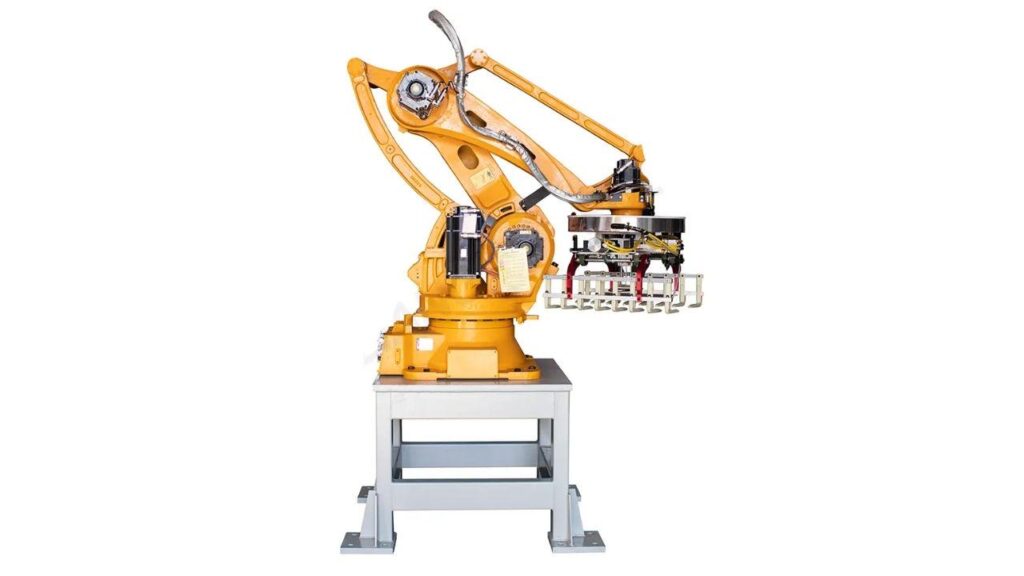
Choosing the right palletizer?
When choosing the right palletizer for your business, consider the following factors:
Determining the production volume
The first step in choosing a palletizer is to determine your daily throughput. Once you know your production requirements, you can determine a palletizer that will efficiently meet your production needs.
Whether you are a high-volume or small-scale producer, the right palletizer will optimize your material handling process, reduce bottlenecks and improve overall productivity.
Evaluate product characteristics
Evaluating the unique characteristics of your product is key to choosing the right palletizer. Consider factors such as the size, shape, weight and fragility of the product.
A suitable palletizer should be able to handle the product safely and efficiently, preventing any potential damage during the palletizing process.
Delicate products may require a gentle touch, while heavy or irregularly shaped products may require a more robust handling mechanism.
Matching the palletizer’s capabilities to your product specifications will ensure a smooth and efficient material handling process.
Evaluate available space
Space utilization is an important aspect of any production facility.
Evaluate available floor space to determine the palletizer that will work well with your production line layout.
Choose the palletizer that maximizes the use of space in the plant to optimize the workflow and create an orderly and efficient work environment.
Flexibility
Flexibility is key in a dynamic industry where product lineups change frequently. Consider choosing a robot palletizer that can be easily reprogrammed.
Robot palletizers have excellent adaptability and can quickly adjust to different palletizing patterns.
Their versatility ensures smooth transitions between different products, increasing operational efficiency and reducing downtime when changing settings.
Safety first
Ensuring the safety of your employees is crucial. Look for palletizers equipped with safety features such as sensors and guards.
These features protect workers from potential accidents during palletizing operations, creating a safe and worry-free work environment.
Reliable suppliers
Choosing a palletizer from a reputable manufacturer or supplier is essential to achieving consistent and reliable operation.
Choose a supplier that offers strong maintenance and technical support to ensure smooth operation and minimize downtime.
Regular maintenance not only extends the life of the palletizer, but also optimizes its performance and reduces long-term operating costs.
Ability to integrate
A well-integrated production line is essential for seamless material handling.
Ensure that the palletizer integrates seamlessly with existing conveyor systems and other packaging machinery.
Streamlined workflows increase overall efficiency and minimize potential interruptions in the palletizing process.
Cost and return on investment
While the cost of the initial investment is an important factor, the expected return on investment (ROI) is also taken into account when choosing a palletizer.
Calculate the potential cost savings and productivity gains to make an informed financial decision that fits your budget and long-term business goals.
User-friendliness
A user-friendly interface is important to minimize the learning curve for employees. Choosing a palletizer with an intuitive interface simplifies operation and reduces training time.
A well-designed interface allows your team to operate the palletizer efficiently, ensuring consistent and efficient material handling.
Room for growth
Finally, consider future growth and expansion plans when choosing a palletizer.
A palletizer that can adapt to changing needs and potential growth ensures a lasting investment.
Future expandability lays the foundation for continued success and minimizes the need for frequent equipment upgrades.
You should do it
Are you ready to buy a palletizer? What are you waiting for? Optimize your palletizing process and increase efficiency with a palletizer!
By considering factors such as throughput, product characteristics, space constraints, safety features and integration capabilities, you can make an informed purchasing decision.
If you need further guidance or have specific questions, feel free to contact our experts and we will provide you with personalized advice. Click on our website to contact us now!
FAQs
What is the purpose of a palletizer?
A palletizer is a machine used to automatically and efficiently stack products onto pallets as an alternative to manual labor.
Can palletizers handle products of all sizes and shapes?
Yes, some palletizers (e.g. robot palletizers) have the flexibility to handle products of different sizes and shapes through simple reprogramming.
Are there different types of palletizers?
Yes, there are different types of palletizers, including robot palletizers, high-level palletizers, low-level palletizers and traditional palletizers.
Which industries benefit from palletizers?
Palletizers are used in industries such as food and beverage, pharmaceutical, consumer goods and manufacturing.
How can I determine the right palletizer for my production volume?
Evaluate your daily production volume and select the palletizer that will effectively meet your production needs.
Are palletizers easy to integrate with existing equipment?
Yes, most palletizers integrate seamlessly with existing conveyor systems and other packaging machinery.
Can palletizers be adapted to the changing production needs of the future?
Some palletizers have the flexibility and programmability to adapt to changing production needs and product lines.
How do you ensure worker safety during palletizer operation?
Look for palletizers with safety features such as sensors and guards to protect workers and prevent accidents.
What role does a user-friendly interface play in palletizer operation?
User-friendly interfaces simplify operations, reduce employee training time and increase overall efficiency.
How do you calculate the return on investment of a palletizer?
The return on investment of a palletizer can be calculated by comparing the initial investment cost with the expected cost savings and increased productivity.